Pass Six Sigma LSSYB Exam in First Attempt Easily
Latest Six Sigma LSSYB Practice Test Questions, Exam Dumps
Accurate & Verified Answers As Experienced in the Actual Test!
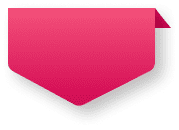
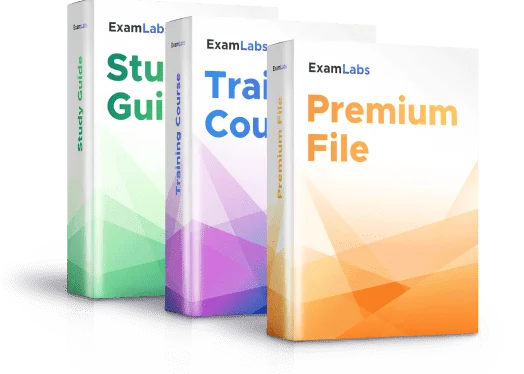
Check our Last Week Results!



- Premium File 150 Questions & Answers
Last Update: Mar 20, 2025 - Training Course 84 Lectures
- Study Guide 382 Pages

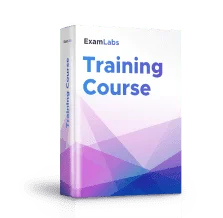
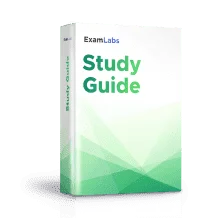
Download Free Six Sigma LSSYB Exam Dumps, Practice Test
File Name | Size | Downloads | |
---|---|---|---|
six sigma |
510.9 KB | 1324 | Download |
six sigma |
83.1 KB | 1430 | Download |
six sigma |
510.9 KB | 1499 | Download |
six sigma |
607 KB | 1488 | Download |
six sigma |
344.2 KB | 2378 | Download |
Free VCE files for Six Sigma LSSYB certification practice test questions and answers, exam dumps are uploaded by real users who have taken the exam recently. Download the latest LSSYB Lean Six Sigma Yellow Belt certification exam practice test questions and answers and sign up for free on Exam-Labs.
Six Sigma LSSYB Practice Test Questions, Six Sigma LSSYB Exam dumps
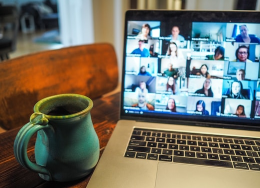
Introduction to Lean Six Sigma Yellow Belt
1. Introduction to Lean Six Sigma Yellow Belt
Hello there. Welcome to the beginning of your Lean Six Sigma Yellow Belt journey. Having now completed all of the White Belt curriculum, you should have learned all of the foundational concepts of Six Sigma if we were speaking in terms of Bloom's Taxonomy. We are now going to advance your skill set from remembering and understanding to basic application and analysis of Lean Six Sigma in the Yellow Belt curriculum. One of the biggest differences you will find in gaining Yellow Belt knowledge is that each topic will begin to move your knowledge beyond basic surface-level understanding. We will learn about fundamentals, like the critical qualities of quality and the cost of poor quality. After we are sure that fundamental concepts have been addressed, we then dive into new areas of the Domaic methodology like the control stage, where we will learn about error-proofing control plans and how to conduct a cost-benefit analysis. This is your first giant leap into SixSigma, and it is an exciting one. So let's begin improving and gathering more solutions for you to ignore your power.
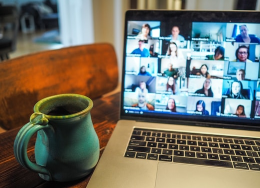
Overview of Lean
1. Overview of lean part 1
Hi there, and welcome to this introduction to Lean. In this overview lecture, we will discuss some of the important concepts, principles, methodologies, and tools involved in a Lean strategy. By the end of this lecture, you will be able to define what a Lean strategy is, what the five main principles of Lean are, how Lean relates to the Toyota Production System, and what the benefits of focusing on waste reduction could be. Well, before we begin our lecture, I'd like for each of you to pause the video for about five to ten minutes. It's.
2. Overview of lean part 2
Welcome back. We're excited to review what it is you know about lean already. In fact, some of you might know quite a bit about Lean. Some of you may be looking into Lean as a strategy, and other of you might be taking the course to improve your professional skill set. Whatever the case may be, we're glad to have you here. Let's get started by discussing some of the various reasons that a company might want to go lean. There are many benefits associated with going lean, and every company will undertake the strategy for various reasons. If you have ever ordered a product online and received it the same day, you most likely ordered it from a lean organization. If you bought a product that all of a sudden cut the price drastically, you may have ordered from a lean organization. It's true. Industries like manufacturing, office, healthcare, agriculture, and education are all ramping up their lean journey to collect benefits like increased efficiency, more market share, increased cash flow, and a better ability to meet customer demands. We can understand these benefits even better when we answer our own question. How do we define lien? Well, formally defined, Lean is a continuous improvement strategy that a company embarks on to maximise customer value and minimize, if not eliminate, all forms of waste. In Lean, we refer to waste as muda. This Japanese term defines any activity that is performed and adds no value to the product or service. Some examples of muta are waiting, workarounds, and rework, which we refer to as overprocessing, transportation defects, and overproduction. It is important to note that while Lean is in fact focused on the elimination of waste, the strategic framework is based on much more. A lean journey can be understood within the framework of a home. We begin first by establishing a solid roof for our home. This roof represents the goals that you are trying to achieve. Whether it's lean Six Sigma or the theory of constraints Most companies would not mind having the highest quality, lowest cost, and shortest lead time. Of course, these goals must be upheld by two pillars. The first pillar that we see is the "just in time" pillar. The "just in time" pillar attempts to have the right product or service in the right place at the right time and in the right amount. Several important concepts are pulled together to create operational excellence like this. The next pillar that supports our goals is the Judoka Pillar. This pillar is focused on building quality into the enterprise with concepts like mistake proofing, visual controls, root cause analysis, and line stops when needed. In order for our two pillars to remain stable and strong, they must be placed on a solid foundation. The foundation of our house is made up of three key elements, which are standard work, load leveling, and Kazen. Together, these three elements create operational stability and give our home a solid structure to stand on. With a home now built, we can begin to create a culture where employees are ready and willing to try new things, express innovative ideas, and create an environment where kaizen is seen and felt everywhere. This type of behaviour and culture comes with one more added accessory to our lean organization: respect for people. Employees must feel empowered, motivated, and supported as the journey moves forward. Without this type of culture, no amount of cutting out waste will make you lean. As a side note, one of the greatest books ever written about lean by Dr. Lyker, which was titled The Toyota Way, outlines 14 management principles for creating a lean organization. Two of those principles spoke directly about developing people. We highly recommend reading this book, as it has become one of the most popular and sought-out books on the topic of lean. Up to this point, you're probably beginning to see how the strategy we call lean has many different levels that it can be interpreted on. Whether our understanding is technical, methodical, or philosophical Understanding Lean without looking into the history of this great strategy would be hard. Over the years, many have embarked on the system that once started in a small town. Shortly after World War II, as the war came to an end, Toyota was struggling financially. They had very little resources to grow on, and their production levels were less than 10% of Mr. Henry Ford's mass production lines. Toyota needed to respond. Tachyono, who was the chief engineer at Toyota, immediately began studying Mr. Ford's methods. Mr. Ono would later go on to create what became known as the Toyota Production System. This system focused on reducing costs by eliminating waste. As time went on, Mr. Ono would later establish many of the tools used in the "just in time" system. Later in 1990, Dr. James Walmart would coin the phrase "lean" during his studies of the Toyota production system for a book titled The Machine That Changed the World. Six years later, Dr. Walmack would author another lean book that outlined five principles, which are now widely accepted as the five core principles of lean thinking. In the book Lean Thinking, we learn that the first principle of a lean organisation is to specify what is considered value and what is considered non-value from a customer's perspective. Once we have a clear understanding of what activities our customers are willing to pay for and what activities they are not willing to pay for, we can then make all the activities in a process visual. This is done by mapping the value stream. The value stream will reveal areas where issues, constraints, and even opportunities may lie in your organization. Next, we make value flow through the value stream by eliminating waste. Dr. Womack then advises that we make value flow only at the request of the customer. In other words, we work based on real customer demand, building the right part at the right time and in the right amount. The final principle reminds us that while it is important to celebrate our small wins and improvements, we must always strive to be better than we were the day before by always pursuing perfection. Well, we have covered a lot about Lean already, but you may be wondering why you haven't heard anything about the Five S system, value stream mapping, or quick change overs. Well, these catchy names that are often associated with Lean are actually some of the most powerful tools used within the strategy. together with concepts like Gen Xi jinbuzu, the Kaizen spirit challenge, respect for others, and teamwork. We arrive in Lean. Well, that wraps up our overview of a lean strategy. As we move forward with learning, you will learn very specific techniques used in a Lean strategy. Remember, my friends, keep on improving, and we will keep on giving you solutions that ignite your power.
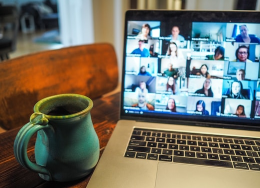
Overview of Six Sigma
1. Overview of Six Sigma Part 1
Hi there, and welcome to this overview of a Six Sigma strategy. My name is Cameron Hanson, and I'll be helping guide you through this overview lecture. In this overview lecture, we will learn where Six Sigma comes from, what Six Sigma means, and introduce the problem solving formula. Let's first start with a discussion. Our story begins back in 1984 with a company by the name of Motorola. Motorola was on the move to create the best products on the market. their competition at the time. General Electric and Walker Telecommunications. But Motorola had a competitive advantage that would soon become known to the entire world. A young engineer by the name of Bill Smith was actively engaged in continuous improvement. Fascinated with how he could improve processes on the production floor, Bill began experimenting with different methods in an attempt to make processes more efficient and effective. Bill believed that by focusing on quality, he could reduce defects in production, which would result in more stable and predictable outputs. During one of his studies, Bill noticed that every business process could be defined, measured, analyzed, improved, and controlled. As time went on, Mr. Smith found that continuing to repeat this method resulted in reduced variations of process outputs, which ultimately helped him to meet customer demands. As time went on, Bill's new method for improving business processes became known as Six Sigma. Now, before we move on, I'd like to know what you know already about Six Sigma. So let's pause the video while you take a few moments to answer the questions on the screen. Go ahead and pause. We'll meet you back here in just a few minutes. Minutes.
2. Overview of Six Sigma Part 2
Welcome back. We hope you had plenty of time to brainstorm and come up with a few answers of your own. Don't forget to send your answers in so a coach can review them. This will help us as we travel along the Lean Six Sigma journey together. Let's jump back in. Formally defined, Six Sigma is a strategy that gives organisations a structured means to improve business processes and solve problems. The result of improved business processes leads to increased performance, reduced defects, reduced variation, improved use of capital, and more stable and consistent processes. When we look at Six Sigma from a technical perspective, we learn that the term SixSigma comes from a statistical background. Sigma is the term used to represent the variance from a standard or average. There are many different Sigma levels. For example, one sigma would represent 6900 defects per million opportunities. But in the case of Six Sigma, the technical definition refers to a performance level of no more than 3.4 defects per million opportunities. So what does this mean exactly? Let's say we were playing a game of darts. A bullseye would represent the absolute perfect game. Because none of us are perfect, we most likely would hit a few bullseyes, and a few might hit some other points on the board. Or worse yet, they wouldn't even come close. Similar to this, most business processes will produce outputs that are defect free.But because our processes, like our skills, are not always perfect, we can assume that some percentage of outputs will contain either defects or be defective. In Six Sigma, we refer to these deviations as standard deviations. You can read the sigma level by first looking at the number, which specifies the number of deviations from the standard, and then at the Greek symbol sigma, which literally means standard deviation. The standard deviation is referred to as a standard because the percentages or amounts that fall into each deviation are generally the same, which gives us the ability to compare the deviation to other data sets. As we noted earlier, in the case of aSix Sigma strategy, the intended goal of a businessprocess is to limit the number of defects tosix standard deviations, or 3.4 defects per million opportunities. Now, if you've been paying attention at all, you're probably thinking, "Wow, that is almost no defect." In fact, as you can see in this chart, six sigma would represent a 99.996% yield rating. Now, you may be thinking, with that type of sigma rating, what will happen to the process over a period of time? Well, as you might have guessed, most processes will develop some variation over time. Let's look at our dartboard for an example. Again, let's pretend for a moment that we were able to hit the target 99.996% of the time. One could assume that over a period of time, your eyes, arms, or hands may become tired from repetition, which would cause a gradual change in the process. Similar to this analogy, most business processes tend to vary over a certain period of time. To account for this shift, or deviation from three to four defects per million opportunities, six sigma uses a plus or minus one five-sigma shift. This helps ensure that the final results are within specified limits. You'll learn more about the Sigma shift as you advance your skill set and understanding of Six Sigma. As you can see, Six Sigma is clearly focused on improving business processes through quantifiable and measurable means. These types of improvements can be quite powerful for an organization. One of the benefits of quantifying and measuring results is that it takes us away from guesswork and assumptions and identifies results based on facts and data. This naturally requires an organisation to gain consensus on metrics and improvement projects all throughout the organization. Along with metrics and consensus, Six Sigma is very focused on developing the talents of people. Six Sigma designates clear roles and responsibilities for people and projects by borrowing from the martial arts belt system. The structure ranges from white to yellow to green to black to the master black belt level. A master black belt is the highest level a Six Sigma practitioner can obtain. Along with these belt levels, the Six Sigma structure also recognises champions within the organization. We will discuss more about the Six Sigma belt structure as you progress in your understanding of this great continuous improvement strategy. There is one more thing we need to cover. But before we move on, let's make sure we understand one of the concepts that were shared in this overview.
3. Overview of Six Sigma Part 3
Well, hi there, and welcome back to our overview of a Six Sigma strategy. You probably have a much better understanding of a standard deviation now and a general understanding of some other very important steps like belt structures, buy-in, and the history of Six Sigma. You should hear back from a coach shortly after they review your standard deviation assignment. Until then, let's move forward. We would like to cover two additional topics that will be a very important foundation for your Six Sigma journey as we move forward. Those topics are the problem-solving formula and the concept of cause and effect. Well, first and foremost, let's begin by discussing the problem-solving formula. We know already that Six Sigma uses statistical analysis and measurement in many different ways. But there is one very simple equation that is at the core of Six Sigma. The problem-solving formula helps us to understand that every outcome is the result of a process being applied to the inputs. In other words, the outputs are determined by the application of specific functions to inputs. Let's look at the formula. There are four essential parts we must consider when solving problems in Six Sigma. First, we must consider why, in our formula, Y represents the desired outcome, result, or goal we are trying to achieve. For example, if we were baking a loaf of banana bread, the banana bread itself would represent our Y. Next, we must consider the inputs, variables, or elements used to create our Y. In our case, the banana bread These inputs are represented by X. Going back to our loaf of banana bread, x would be the ingredients we use to make the banana bread. Now, having a goal and some inputs alone will not create or transform our XS into Ys. To do this, we must apply a process as a means of transformation. This transformation processor is represented by F. F represents the function or process being applied to our ingredients, which ultimately modifies, changes, transforms, or alters the ingredients into banana bread. Well, hopefully it does. Like we saw earlier when we discussed throwing darts, things don't always turn out the way they should or the way we want them to. Because of this, we have one more important part of our problem-solving equation, which helps us account for some level of error or difference from our X. This is shown with a Greek letter, epsilon. As noted earlier, Epsilon helps us account for unseen changes in our banana bread. For example, if we made five loaves of banana bread, we may use a slightly lower heat setting, a different amount of a specific ingredient, or we may cook the bread a few minutes longer or shorter than we did before. Of course, the end result is banana bread, but each loaf of our banana bread will have some difference or variance from the other loaves. This variance is represented by Epsilon. In a nutshell, Y equals FX plus Epsilon tells us that all outcomes are determined by the way inputs are transformed according to said processes. This same concept runs through the cause-and-effect philosophy, which tells us that all inputs, process functions, and even errors will affect the outcome in some way. Looking back at our banana bread, we can see that if we change our inputs or certain areas of the process, we will in fact end up with a different result or why.This introduces to us what is known as "cause and effect." Let's look back at our banana bread one more time before we wrap up. We now know that if we change some elements in our Y equals FX plus Epsilon formula, it will have an impact or effect on the outcome. As you can now see, the cause shows us why something happens, and the effect tells us what happens. When we apply this concept to Six Sigma, it allows us to then look at a process and see how the process will allow for variation. Well, that is a lot to take in, I know. But don't worry, we will be diving deeper into each of these concepts as you progress and advance on your lean Six Sigma journey. Remember, this is just an overview of Six Sigma. Now, before you go, there is a fun activity for you to work on, and hopefully you'll end up with a tasty treat at the end too. So be sure to complete the activity. Take your quiz as is and keep on improving while we keep on giving you solutions that ignite your power.
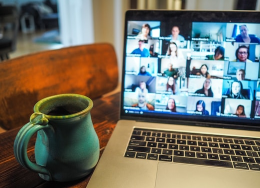
Overview of Continuous improvement strategies, Six Sigma and Lean – DEFINE
1. Overview of Continuous Improvement Strategies (Define)
Well, as we stated before, today we're going to be talking about continuous improvement. Now when we finish up the fund today, you will know just exactly what continuous improvement is and why others embark on continuous improvement journeys. You'll also have an understanding of what the four major improvement strategies are. We will also mention some of the more common tools used in continuous improvement initiatives. Lastly, we will talk about the five core principles, usually defined in lean but universally applicable to all strategies. Well, first let's start off by answering a question: Why would anybody want to invest in continuous improvement? One of the first and most well-known reasons is that no matter what business you are in or part of, your industry is most likely in no way at a standstill. They're actually quite dynamic. Given this universal knowledge, processes need to be relentlessly refined over and over again. The next reason can be compared to a high jumper. If you broke a record in the high jump, it wouldn't make any sense at all to not try and jump even higher than before. Similarly, organisational processes must be improved rather than simply reviewed and audited. Unless, of course, you don't mind the next big company jumping a little bit higher than you. Another fairly common purpose is to achieve defined objectives and goals that may have fallen off track somewhere in your journey. As a side note, continuous improvement is often associated with quantitative measures that track progress toward objectives and the end goal. Along with this common reason to embark on continuous improvement, oftentimes companies do it just to get better and improve productivity. One last purpose for embarking on continuous improvement is for the way it improves worker satisfaction, workplace safety, and your unique approach to developing and empowering your most important resource, your employees. Now there are most likely many other reasons to embark on one of the four major strategies under the continuous improvement umbrella. But in general, the main reason is: given the opportunity, who doesn't want to improve? Well, now that we understand some of the key purposes of embarking on and investing in continuous improvement, let's answer the question: Just what is continuous improvement? Now continuous improvement can be defined as theact of making regular incremental improvements that assistorganizations in transforming, evolving and upgrading processes, productsand services in pursuit of excellence. Continuous improvement was originally noted for its absolutely powerful effect on manufacturing. But today it has evolved into many industries, such as health services, government, and just about any other industry that you can think of. Now with that said, try to think of continuous improvement like an umbrella. When you open up an umbrella, there are a few prongs that cause it to hold its shape when the rain falls. Those prongs represent the strategies that fall under the continuous improvement umbrella. Our umbrella needs only four prongs, or strategies. Those four strategies of continuous improvement are lean six-sigma, total quality management, Management and the Theory of Constraints Liaison can be described as an excellent strategy that includes both quality and process, product and service, as well as a heightened ability to remove waste from every aspect of an organization. Lien does this by attacking eight major forms of waste in service and in manufacturing. Those eight forms of waste are referred to as "mooda" in a lean environment. Additionally, LIEN bases its activities on five core principles. These five core principles are as follows: identifying value from the customer's perspective; mapping out the value stream; making value flow at the customer's poll; responding only to the customer's needs; and striving for perfection. By implementing lean—and we mean really implementing it—organizations can reduce the need for working capital, increase inventory turns, gain more market share, increase profit margins, develop a highly skilled, empowered workforce, and produce products with absolute perfect quality. Along with Lean, Six Sigma is a strategy that aims at achieving absolutely zero defects. In other words, near perfect processes, products, and services. We can define Six Sigma as a strategy that entails the use of tools and methodologies for the improvement of organisational processes. Now, additionally, we should add that the intention of Six Sigma is to decrease process variation and improve quality. Now, to become a Six Sigma organization, the goal is to produce no more than 3.4 defects per million opportunities. Three key elements to reach the Six Sigma level are your customer, your processes, and your employees. Companies that begin implementing Six Sigma in their organisation can expect to see reduced process variations, significant improvements in quality, and savings that could put everyone on a six-figure salary. Well, the next strategy in our continuous improvement umbrella is total quality management. Now, officially, Total Quality Management is an approach that management takes to maintain or improve customer satisfaction. Like the other strategies, TQM, or Total Quality Management, requires the participation and involvement of the entire organisation to change processes, products, and the culture within your business. There are four key ideas in total quality management. Those four ideas are number one: a commitment from management and participants to the strategy. Number two, the concept of continuous improvement is understood by everyone, and the culture of continuous improvement is embraced by everyone. Third, appropriate metrics have been implemented to measure and track your progress toward objectives. And lastly, number four, there are no adversarial relationships. Customers and suppliers are connected and strive to support one another. The final piece of our umbrella is the theory of constraints. The theory of constraints is widely accepted. In fact, it can be applied to just about any organisation that has humans in it. The core idea behind the Theory of Constraints is that just about any system or process will contain at least one constraint that will limit the maximum output of that process or system. since it makes no sense to operate any part of the process quicker than the slowest part. The theory of constraints seeks to remove constraints so that processes can operate at their full speed. The general strategy of the theory of constraints focuses on five repeatable steps. Those five steps are number one: identify the constraint. Number two, expose or exploit the constraint. Number three, adjust other processes to function with the newly removed constraint; number four, elevate the constraint; and number five, repeat the cycle over and over again. Well, those are the four major continuous improvement strategies used in transforming organizations. Keep in mind that each of these strategies uses a set of highly developed methodologies and tools to help them accomplish the tactical side of the strategy. We would like to mention five different tools that are commonly used in Six Sigma so that you have a general idea of what some of the tools may be. Now, as we develop into later courses, your skillset will undoubtedly transform as we dig into many important tools within the continuous improvement umbrella. The five tools we will introduce today are the first of the seven basic tools. Number two is the five-S system. Number three: value stream mapping. There are four pull systems. And Kanban. And lastly, we'll introduce the single-minute exchange of Die, also known as Smed. Well, to start, if you haven't seen our Seven Basic Quality Tools video, go and watch it. Or take our Lean Six Sigma White Belt course, which introduces and includes an overview of the seven basic quality tools, just to keep you up to speed. The seven basic quality tools are: number one, the process map; number two, the control chart; and number three, the paradox chart, also referred to as the parado diagram. Number four is the Cause-and-Effect Diagram, commonly referred to after its founder as the Ishikawa Diagram number five. the histogram number six, the check sheet, and last but not least, the scatter chart. The tools can be defined as seven and, when applied appropriately, assist organisations in understanding and evaluating their processes with the intention of improving them. The next tool we will introduce to you is a more common one that you may have heard of already. The tool is called Five S, and it's really more of a system than just a tool. The Five S is referred to as a form of workplace organisation that assists workers in optimising the efficiency and effectiveness of their area while creating a safe, neat, and orderly environment. Additionally, if you have an area that is in good Five-S condition, any abnormality will stand out right away. The Five S's stand for sort, set in order, sometimes referred to as simplify, shine, standardize, and last but not least, sustain. Along with efficiency and tidiness, Five S creates a basis for lean thinking and is often a great tool to begin bringing people together and taking down the silos that sometimes form in organizations. Last but not least, Five S pairs very well with many other tools, such as SMED or Kanban. The value stream map identifies value added andnonvalue added activities while capturing other key piecesof information within the value stream. Some common reasons to use a value streammap would be to lead a waste reduction project, decrease cycle times, and make the process flow more efficiently and effectively. There are three different levels of value stream mapping: a process level value streammap, a door-to-door level value streammap, and the extended enterprise value stream map. Now, the next system that is very popular in terms of continuous improvement is the poll system. A poll system assumes that we only produce or develop items or services in response to a demand or to replace those taken for use elsewhere. The Kanban is a very effective pulsing tool.
Six Sigma LSSYB Exam Dumps, Six Sigma LSSYB Practice Test Questions and Answers
Do you have questions about our LSSYB Lean Six Sigma Yellow Belt practice test questions and answers or any of our products? If you are not clear about our Six Sigma LSSYB exam practice test questions, you can read the FAQ below.
Purchase Six Sigma LSSYB Exam Training Products Individually

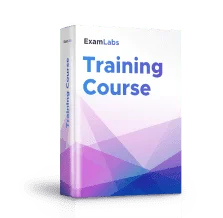
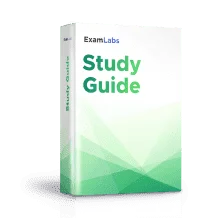

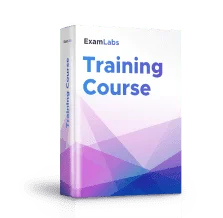
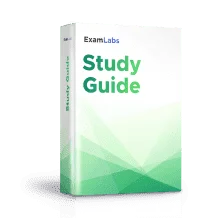